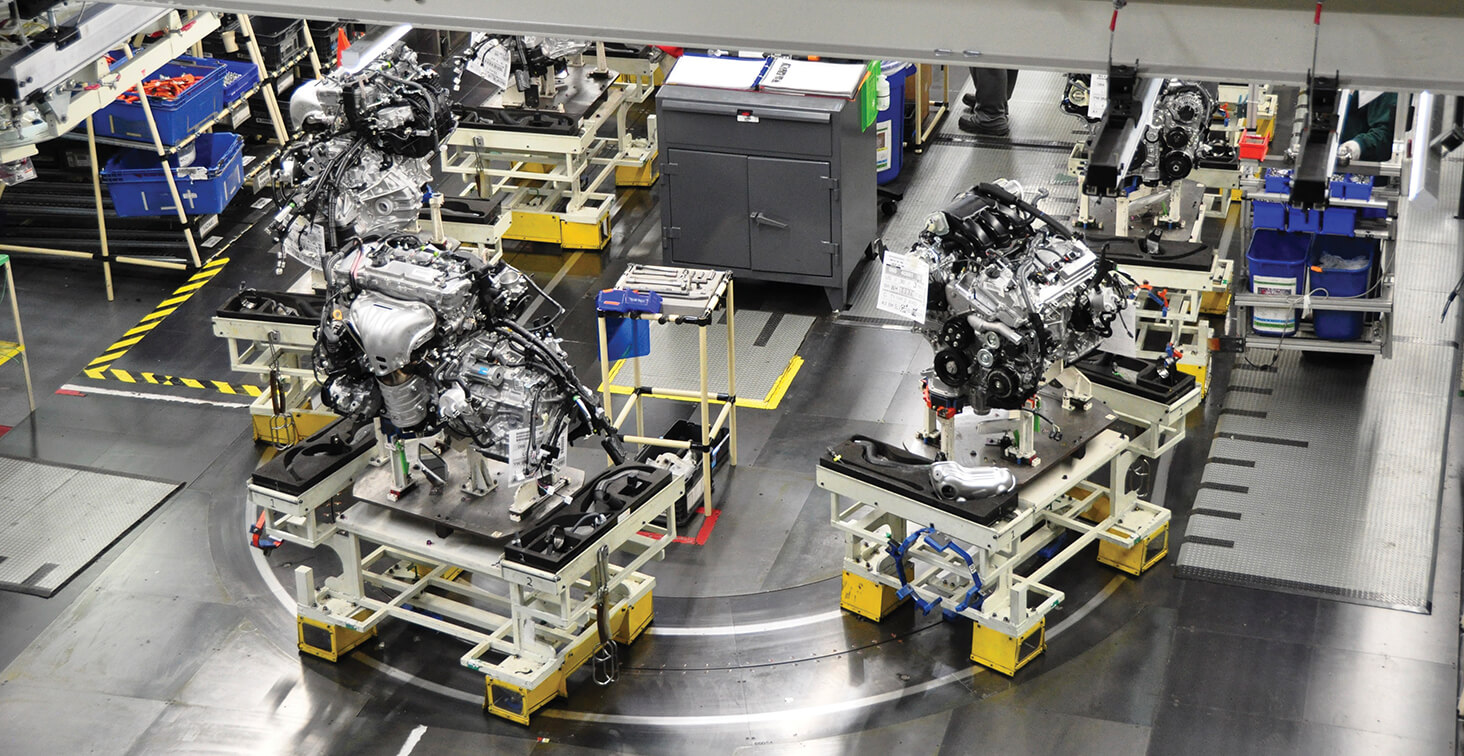
Collision Pros Magazine 2018 | ISSUE 2
Toyota Rethinks How to Build Vehicles
A CASE WHERE LESS IS MORE
As a collision repair facility, you must work on a variety of vehicle body styles as well as different chassis configurations (unibody as well as body-on-frame). To streamline the development of new models, as well as to make them easier to repair, Toyota has been on a mission to reduce the number of architectural platforms used to build new vehicles.
INTRODUCING TOYOTA NEW GLOBAL ARCHITECTURE
Up until recently, Toyota had 105 different architectural platforms. Now, thanks to Toyota New Global Architecture (TNGA), the number of platforms will be reduced to five.
Just as athletes build their core strength to maximize their performance, Toyota is working on improving the vehicles’ core components. To accomplish that goal and to enhance each model’s unique features, these new platforms will share their highly functional core components.
The end result will be vehicles that deliver improved agility and dynamic performance thanks to possessing a stronger core. They will be compact, but efficient, and feature progressive design. This is a total rethinking of how to build vehicles: It’s about building better vehicles on common platforms with common parts. The aim is to make Toyota’s manufacturing plants more flexible and responsive to changes in the marketplace. This flexibility will lead to cost savings that can then be reinvested in future technologies, giving rise to the next generation of Toyota vehicles. Accomplishing these goals will also make these new models easier for your shop to repair as it will only have to be proficient with these five platforms.

to drive
traditional spot welding also
contributes to a stronger chassis.
keep on driving by creating an
enjoyable total sensory experience.

THE FOUNDATION OF TOYOTA NEW GLOBAL ARCHITECTURE
The platform is the basic core around which the rest of the vehicle is built. In addition to more than a hundred different platforms, globally Toyota currently uses more than 800 different powertrains, including engines modified to fi t those different platforms. By adopting TNGA, Toyota can cover the entire range of vehicles—from compact sedans and sports cars to SUVs—with just five platforms.
In addition, all key interior components such as steering wheels, gear shifters, pedals and airbags will be dictated by five standardized seat heights. Designers will select a seat height and the vehicle’s purpose (whether it’s a sedan, sports car or SUV), which will lead to a concise decision tree of accompanying components. Then, thanks to unique interior finishes combined with bold exterior styling, this simplification of the platforms becomes invisible. That’s because TNGA is built on two pillars: core strength and emphasized personality.
Core strength relates to increased chassis stiffness and a lower center of gravity to improve the basic performance of the core (or essential) parts and raises the level of all Toyota vehicles. And by sharing high-performance components, chief engineers are able to focus on accentuating the appeal of each model, giving them more personality.
Using standardized platforms, powertrains and major components will help Toyota make cars that require fewer resources to build and provide a safer and more enjoyable drive with even greater fuel efficiency.
EXAMPLES OF TNGA IN ACTION
The 2017 Prius represents the first vehicle built with TNGA. The result is a vehicle that is more powerful and fuel efficient, produces lower emissions, and weighs less thanks to the use of lighter materials. In addition, this Prius delivers enhanced visibility and legroom and features a lower and wider stance, more responsive steering, and improved ride and handling, all with more athletic and aggressive styling.
The 2018 Toyota Camry is the first North American TNGA assembled vehicle.
Moving forward, TNGA will help shorten the development cycle for vehicle improvements and getting new vehicles to market.
TNGA SEGMENTS
Currently, there are two primary TNGA segments:
- GA-C Platform—applied to the fourth-generation Prius, second generation
Prius Prime (PHEV), 2018 C-HR and the upcoming 2019 Corolla
- GA-K Platform—applied with the 2018 Camry and 2019 Avalon
The aim is to make Toyota’s manufacturing plants more flexible and responsive to changes in the marketplace. This flexibility will lead to cost savings that can then be reinvested in future technologies, giving rise to the next generation of Toyota vehicles.
TNGA LEADS TO NEW ASSEMBLY TECHNOLOGIES
In refining the design and manufacturing process, TNGA has led to the adoption of various new technologies:
- Paint shops are designed to use less water and reduce plant waste by shifting to lower-sludge-producing metal oxide phosphate paint chemicals.
- Shared parts and components mean multiple vehicles can be assembled on the same line.
- Hot stamping and new adhesives create a stronger, more rigid chassis.
- Laser screw welding instead of traditional spot welding also contributes to a stronger chassis.
Another example is bumper production: A new plastic mold machine makes one-piece bumpers using new adhesives that improve body stiffness, which contributes to better handling. And, this machine can produce a Camry bumper, then an Avalon bumper, then a Camry bumper based on production demand vs. batch production, improving assembly line flexibility.
TNGA’S FIVE DOMAINS
TNGA affects owners in these five areas:
- Driving Quality: Making vehicles that are satisfying to drive
- Comfort: Comfort that makes drivers want to keep on driving by creating an enjoyable total sensory experience
- User-Friendliness: Smart technology that enriches the daily driving experience–including everything from luggage space to fuel consumption
- Pride of Ownership: State-of-the-art environmental performance teamed with sophisticated styling
- Security: Creating a strong body that protects the driver and passenger, then adding world-class security features
What TNGA Means for the Collision Repairer
Through TNGA, Toyota is revolutionizing the manufacturing process. It also represents a pioneering of the design and development of future automobiles for the coming decades. Put simply, a greater focus on standardized parts and components means Toyota’s future vehicles will be more attractive and more engaging to drive. They’ll be easier to design and develop and will deliver more quickly. What it means to you, the collision repair facility, is that it’s also more efficient for you to repair vehicles, as you’ll be working with only five basic platforms. Fewer repair procedures and simplified repairs—proof that less is even better than before.